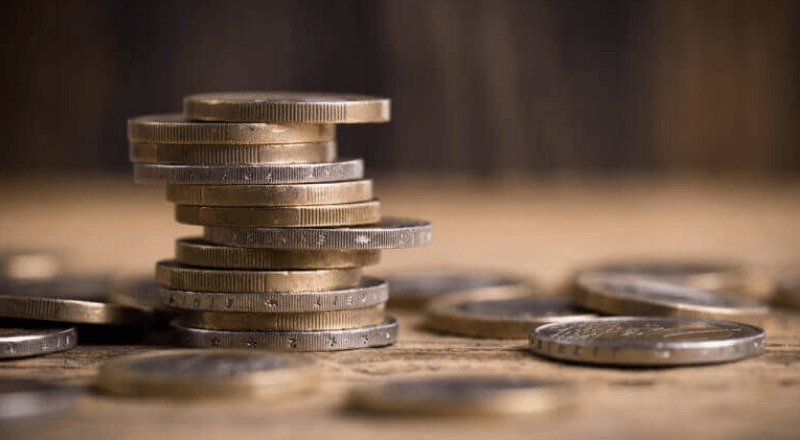
- About Us
- Investor Relations
- Our Businesses
- Our Investments
- Sustainability
- Blog
Kuwait-based Agility Logistics Parks customers can log-on to view contracts and make payments.
UK MOD personnel can log-in to the GRMS portal to schedule household relocation shipments.
Kuwait-based Agility Logistics Parks customers can log-on to view contracts and make payments.
UK MOD personnel can log-in to the GRMS portal to schedule household relocation shipments.
Agility’s take on the supply chain, emerging markets, sustainability and more
Trade is an important aspect of Africa’s economic growth and development, helping the continent address numerous socio-economic challenges while opening …
Read More →Trade is an important aspect of Africa’s economic growth and development, helping the continent address numerous socio-economic challenges while opening …
Read More →Africa is making small strides to upgrade its logistics infrastructure. Leveraging eco-conscious technologies and innovative solutions, Africa has joined the initiative of developing sustainable logi...
Read More →Egypt is one of the countries standing at the threshold of economic transformation driven by logistics and innovation. At the …
Read More →The Suez Canal is a vital hub for international trade, connecting the East and West by linking the Mediterranean and …
Read More →As I head to Saudi’s FII conference, known as “Davos in the Desert” this week, I am reflecting on the pace of change I’ve personally witnessed in KSA. Saudi Arabia’s progress in its jour...
Read More →Egypt has undergone serious development in the past couple of years, especially concerning its historical and cultural structures. But at …
Read More →The Middle East/Gulf Cooperation Council (GCC) region has been a subject of tremendous growth and development in recent years. This …
Read More →At the 2023 WTO Public Forum, Agility's Tarek Sultan joined a panel that explored the opportunities and challenges to facilitate the movement and take-up of zero- and low-emissions technologies in tr...
Read More →Data centers are often thought of as the backbone of the internet, and for good reason. Without data centers, we …
Read More →EDGE certification is a much-discussed topic in today’s warehousing industry, especially as the sector strives to become more sustainable, efficient, and eco-friendly.
Read More →The Suez Canal in Egypt is an essential location for maritime trade, providing a strategic passageway for vessels to travel …
Read More →The International Finance Corporation (IFC), a member of the World Bank Group, developed the Excellence in Design for Greater Efficiencies (EDGE) certification system to encourage and reward builders...
Read More →Anyone who has shipped internationally in the past knows the customs clearance process can be time-consuming and complicated. This is …
Read More →The Suez Canal Economic Zone is a testament to Egypt’s efforts to become a key player in the global economy. …
Read More →Sustainable Aviation Fuel (SAF) is becoming increasingly important in the efforts to reduce aviation’s impact on the environment. As more and more people are taking to the skies, airlines worldwide...
Read More →Scope 1, Scope 2, and Scope 3 emissions are terms used to categorize different sources of greenhouse gas (GHG) emissions associated with an organization’s activities. These three categories are def...
Read More →